Introduction
Bushings, as a component with high dielectric and thermal stress, are of great importance for the reliability of transformers. According to general statistics, bushings are involved in an average of about 14% of transformer failures. Reliable bushings have among others the requirements: Personal protection object protection and ecological aspects, to fulfill. In the design, therefore, the design, choice of materials and the quantity of materials used are decisive.
To improve the stress distribution, OIP/HP/RIP/RIS are used as the main insulation. These insulations are very manufacturing and technology intensive and are naturally subject to aging. These capacitively controlled bushings must also be periodically checked for aging and functionality via a 3 kV measuring tap. The tan-delta measurement provides information about the condition of the main insulation. The capacitance measurement provides information on potential control and the condition of the individual capacitors.
In the drawing SB 2219 the comparison between simpler geometrical electric field controls, DIN porcelain bushings, SIDI-ECO and capacitor bushings can be seen.
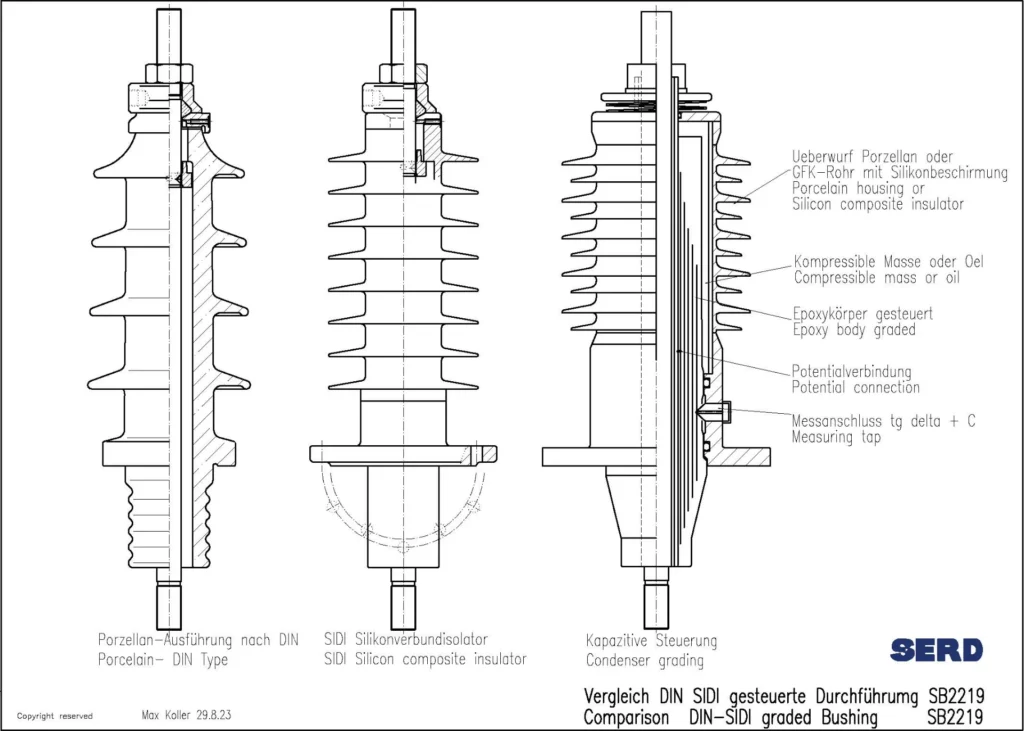
Undoubtedly, simple geometric control, if properly designed, is as reliable and significantly less aging than OIP / HP / RIP / RIS main insulation with concentric condenser linings.
The research indicates that geometrically controlled feedthroughs using modern materials and manufacturing methods can provide ecological solutions. In addition, modern designs with composite insulation provide better protection for people and property than porcelain insulators (porcelain particles fly into the environment if the bushing is destroyed).
Available in the voltage range up to 52 kV, SIDI-ECO type bushings are of high quality and reliability and are comparable with more complex controls of the bushing capacitor coatings.
Tightness / pressure resistance / explosion safety
The chosen design of the SIDI-ECO insulator proved to be helium-tight <10-6 mbar l/sec in tests with 5bar overpressure. The explosion safety could be demonstrated in a water pressure test in comparison with a DIN porcelain insulator. As Figure 1 shows, the porcelain insulator was already leaking and damaged at pressures below 2.5Mpa. The silicone insulator remained tight to above 6Mpa. The burst pressure was not reached with the silicone insulator because the maximum permissible pressure of the test vessel was reached.
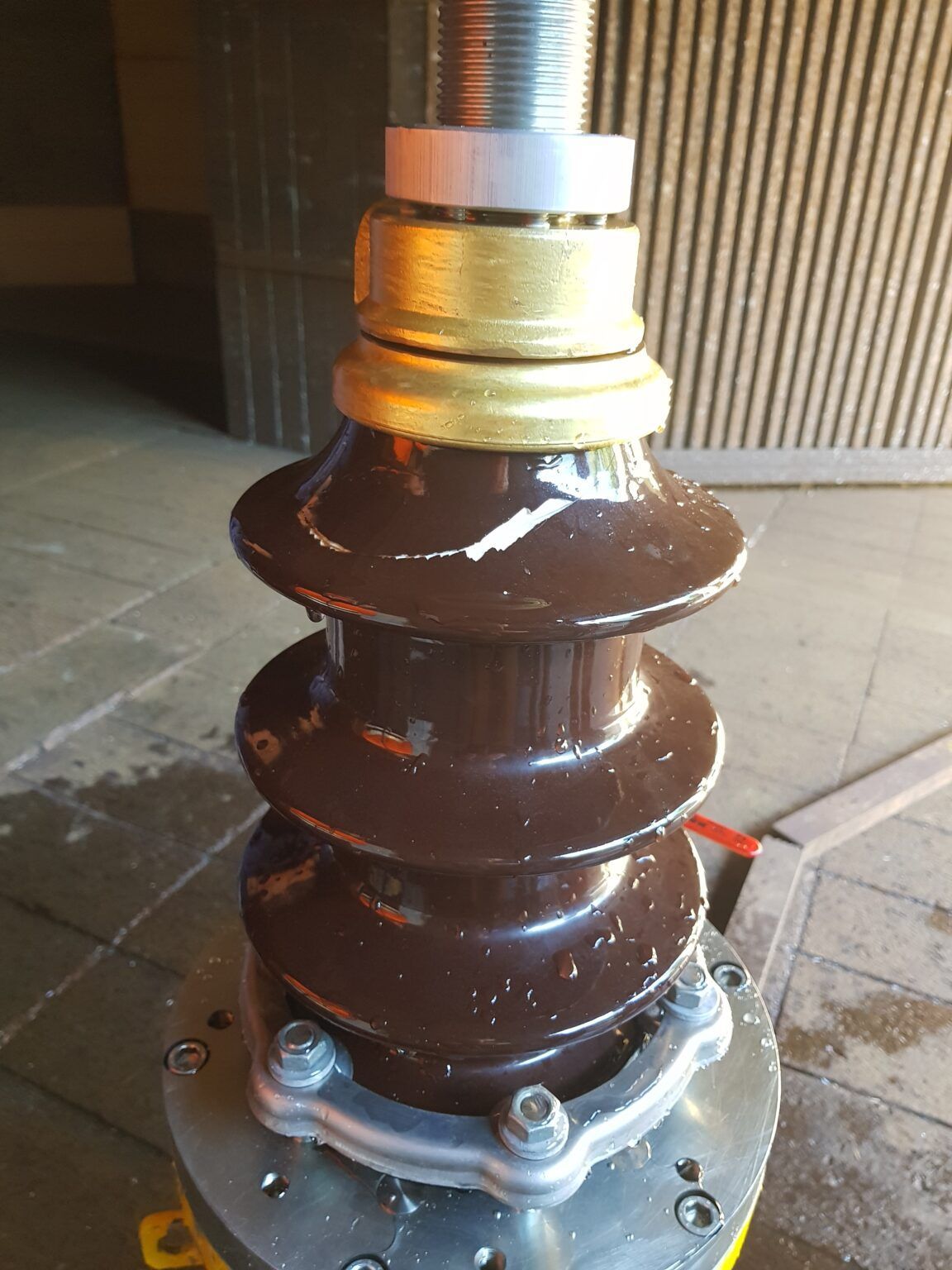
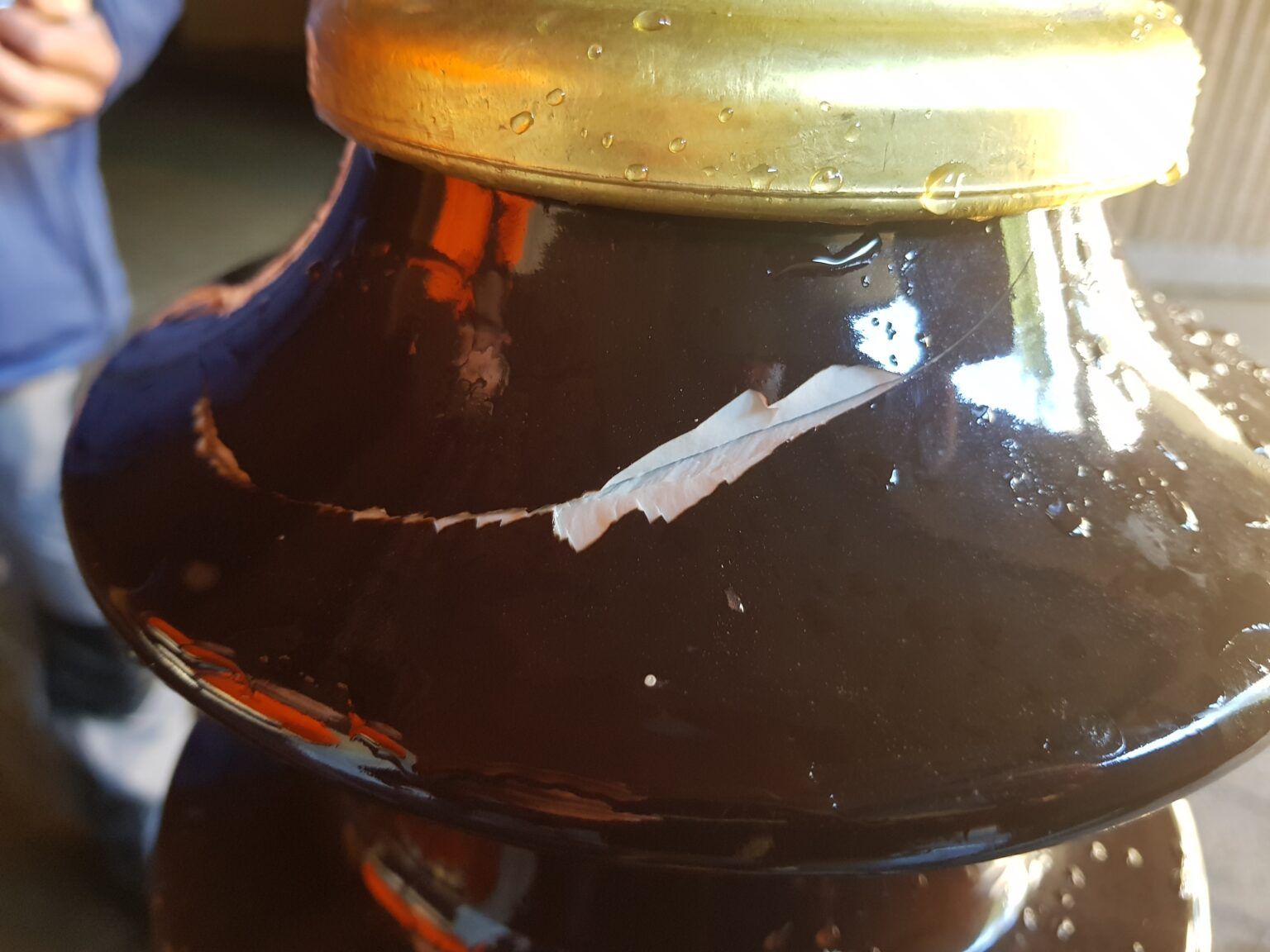
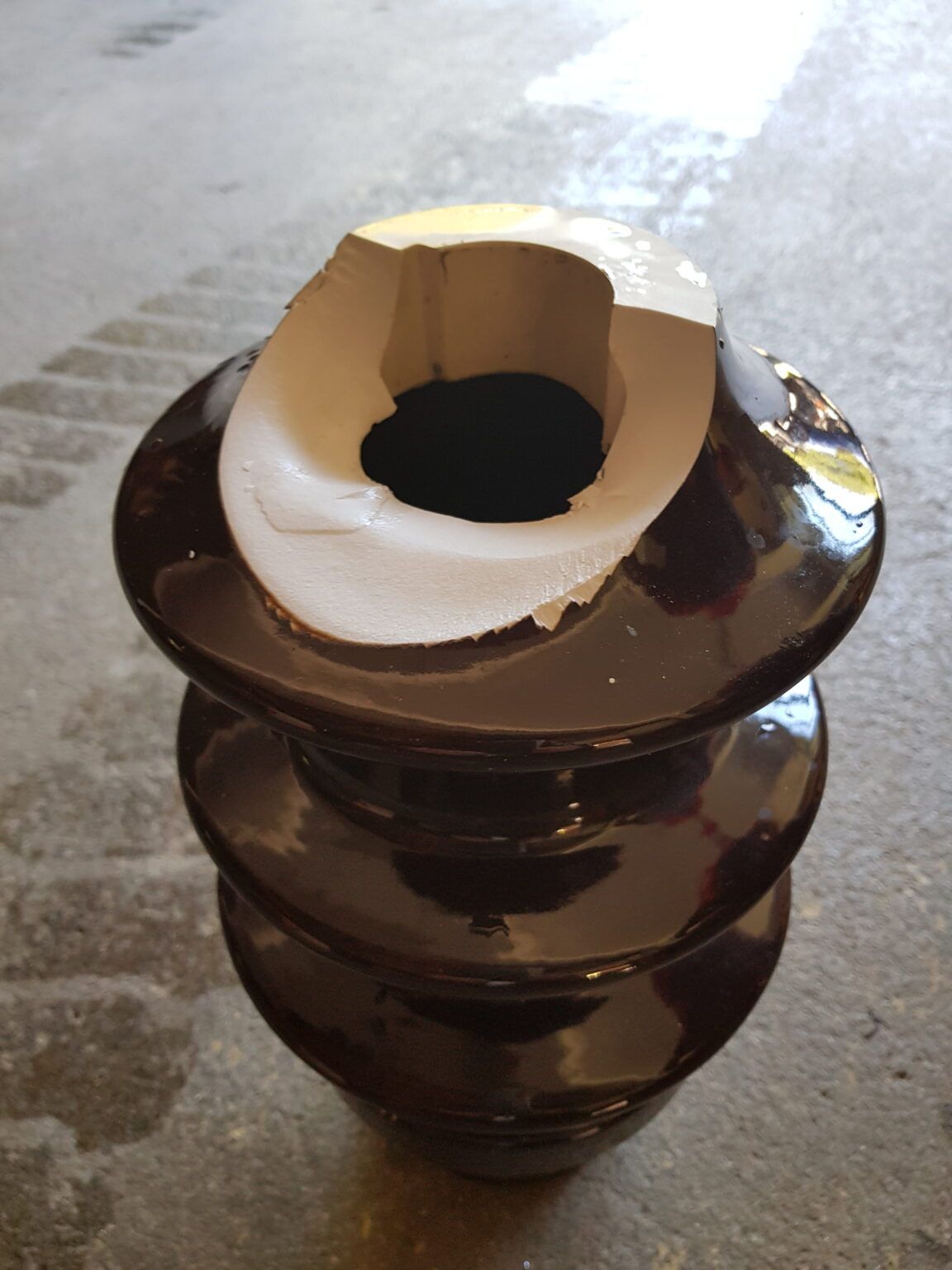
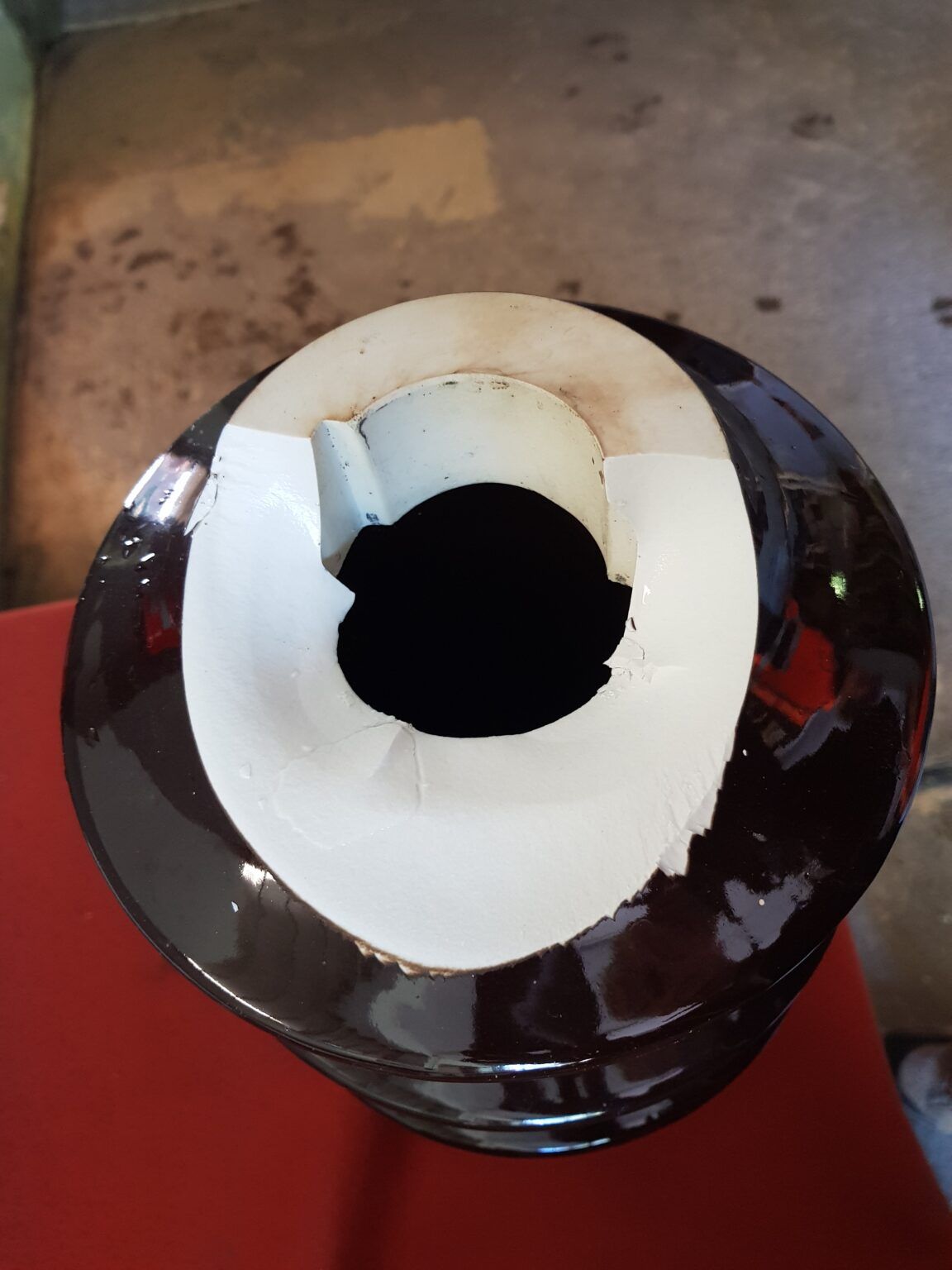
Water pressure test , porcelain and silicone insulator
The compression test shows that the SIDI-ECO bushing plays an important role with regard to explosion safety.
Design analysis
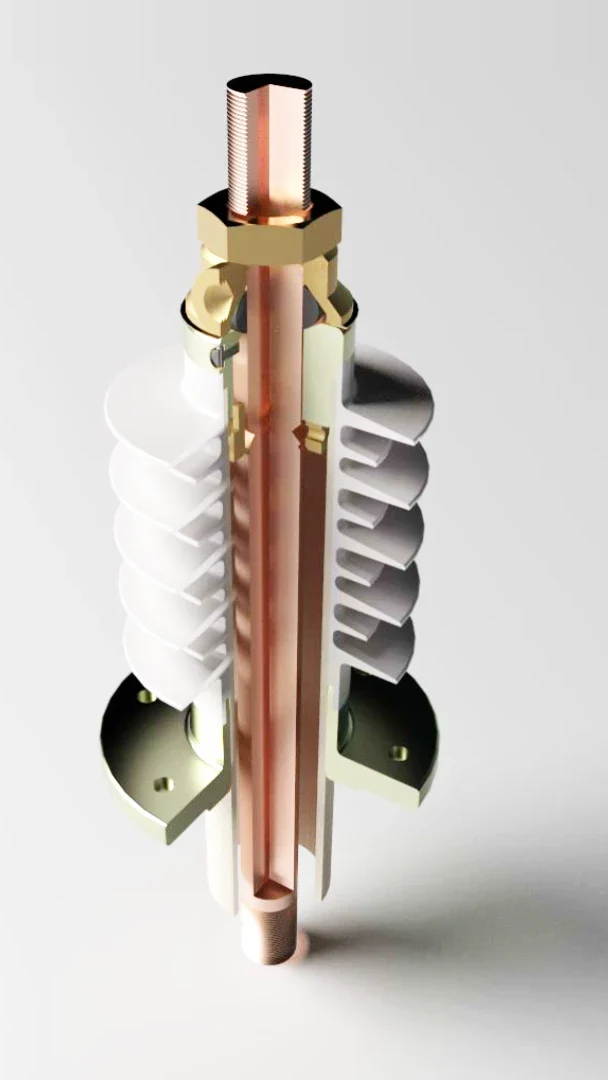
Electric field control through geometric component design of all field-relevant areas can be achieved for such bushings during design using modern calculation programs. Figure 2 illustrates the structure of the bushing. The basic design corresponds in individual areas to the familiar DIN bushing with porcelain insulator.
However, the porcelain insulator is replaced by a dielectrically high-quality epoxy – glass fiber composite tube with cast-on silicone insulation. The fixation of the inner conductor is done with the help of the fitting design known and proven from the DIN implementation. The insulation inside the insulator is formed by the liquid insulating material (e.g. insulating oil) of the transformer. The bushing is open to the transformer vessel to the connection, so that some heat circulation of the insulating liquid is allowed. Aging of the internal insulation is therefore possible at most in the event of severe aging of the transformer filling fluid.
Electric field and voltage distribution
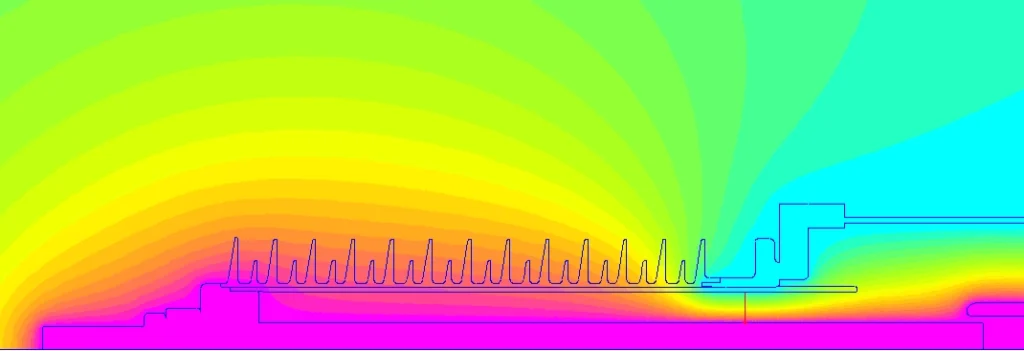
The electric field curve based on the voltage distribution, both in axial and radial direction starting from the central current conductor, is illustrated by figure 3.
The optimization with the help of the field image analysis allows a locally controlled voltage distribution geometrically determined by the design of the components. The radial field distribution in the area of the flange is controlled proportionally 1/ln r/r1 and the quasi-homogeneous field with highest field strength at the inner conductor in the liquid insulation. The axial field distribution outside the flange area, on the other hand, is essentially determined by the flange design. More detail on the field section in the flange area is shown in figure 4 on the basis of the field lines.
In the case of field area A in the conductor-flange area, the gradient is greatest in the inner conductor and, near the flange, in the outer field area B. The stress on the outer insulation in the silicone insulator area is then rather moderate.
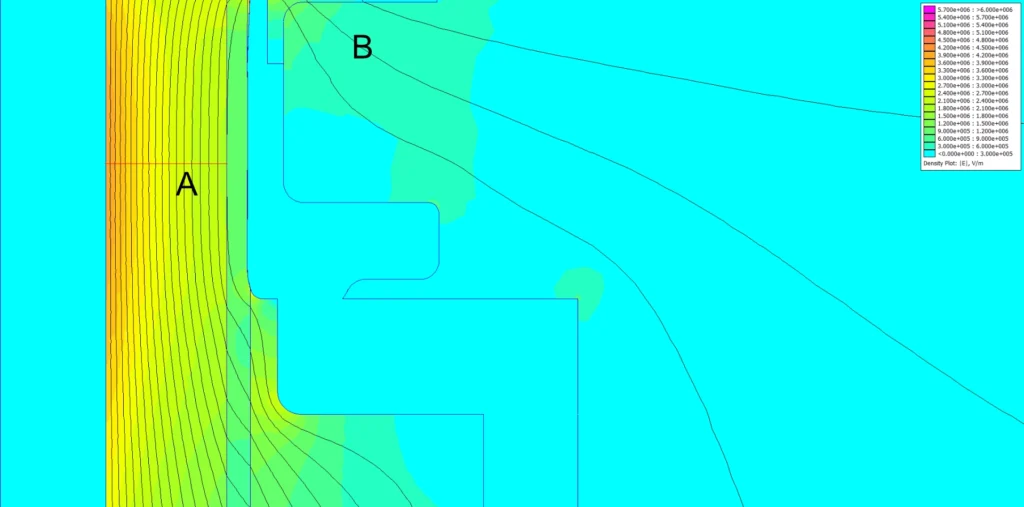
The oil gap between the inner conductor and the insulator in area A is designed with sufficiently high safety. Even with gas-saturated oil, the full test voltage is maintained. The strength under lightning impulse is not critical due to the slower streamer development in the oil, compared to AC.
The tangential stress on the silicone screens is practically consistently below 0.25 kV/mm during operation. This is illustrated by figure 5 using the field strength along the length of the insulator. Where this low value is exceeded, however, the affected length is less than 10 mm. Thus, aging of the silicone insulator by water drop corona is excluded.
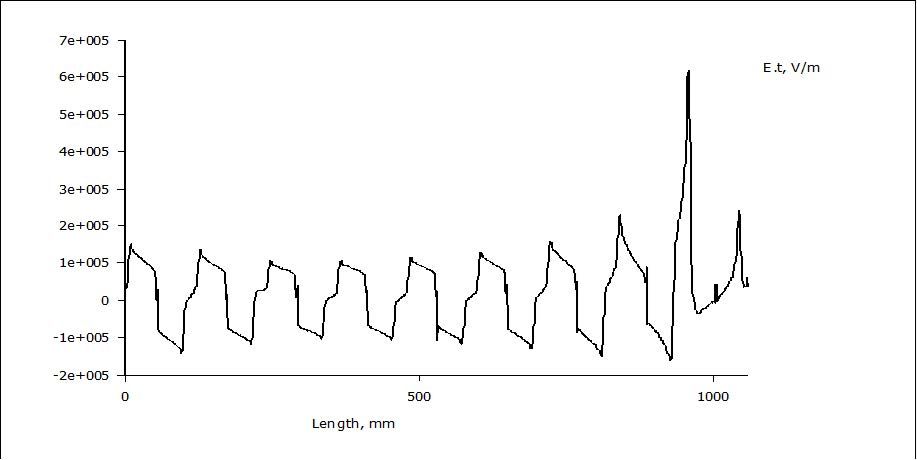
The silicone composite insulator (SVI) is a design that has been proven in principle over 25 years across the entire voltage range for AC and DC. The silicone is cast onto the primer-treated surface of an epoxy fiberglass tube. After vulcanization, the silicone and the carrier tube body form a chemically physically bonded unit. The elasticity of such insulators and the temperature resistance of the materials are tested by bending stresses and with temperatures above minus 60°C. Silicone can withstand the greatest temperature variations and is extremely climate resistant with over plus 200°C and can withstand temporary loss of elasticity even at temperatures lower than minus 70°C. The composite isolation used for the SIDI-ECO bushing can be recycled without any problems.
Silicone properties
Silicone as a material molecule does not contain carbon, only silicon and oxygen atoms form the primary material chain. The molecule of the material contains only in the outer groups some methyl compounds with low content of carbon. Virtually no semiconducting discharge traces are formed in the presence of pollution and electrical discharges.
Silicone is the only known polymer material with high water repellency (hydrophobicity). When the surface is moistened, only single drops of water are formed. While other materials lose their hydrophobicity completely over time, silicone regenerates continuously in this respect and, according to studies, the hydrophobicity of silicone is retained for over 40 years. The water repellency, which is reduced over time due to adhering impurities, can be substantially improved again, up to the level of the new condition, by suitable cleaning of the surfaces. In case of strong erosion of the surface by windblown sand, it becomes rough but remains hydrophobic. The material is stable against UV radiation.
Closing words
In 2001, several power plants and transformer manufacturers approached the newly founded SERD GmbH with the request or order to develop a bushing that, among other things, the requirements: Personal protection, object protection and ecological aspects, and 100% interchangeable with DIN porcelain bushings.
In 2002, the first prototypes were manufactured and successfully tested. Shortly after, the first SIDI-ECO bushings for 24 kV were used both for new transformers and for the replacement of DIN porcelain bushings in the field. Since 2002, more than 3500 bushings are successfully in operation worldwide.
For more information, please contact us at info@serd.gmbh.ch.
Schleinikon, August 2023 / WSPC